With the popularization of mechanization and informatization, relying on the development of the Internet of Things, big data and autonomous driving technology, manufacturing companies have begun to move toward intelligence. As the material and data carrier of smart logistics in the field, industrial mobile robots have gradually been recognized and applied on a large scale by various industries. They not only alleviate the pressure of manufacturing labor shortages but also improve production efficiency and improve the data collection process. It has an epoch-making impact on production management and logistics scheduling.
CASUN has focused on the AGV industry for 14 years and has won recognition both inside and outside the industry with its advanced technology, complete product series, rich implementation experience, and stable delivery system. Especially in terms of product performance, it is constantly iterating and optimizing based on customer needs and on-site implementation experience and has always maintained its leading position in the industry. Taking the two-dimensional code navigation technology as an example, the backpack-lifting AGV of CASUN two-dimensional code navigation can run at a speed of 1.5m/s, and the docking accuracy can reach ±5mm, which can realize intelligent sorting, cluster scheduling, intelligent route planning, etc. A variety of functions.
A few days ago, the warehouse site of a large tobacco company is applying the CASUN intelligent C2-23 piggyback AGV to realize the function of intelligent storage and sorting.
Contents
Background of the project
In this project, the AGV is mainly used in the finished product warehousing process. The AGV is used to complete the intelligent sorting and cooperate with the robotic arm to realize the unmanned warehousing operation of the finished product automatically warehousing.
Project difficulty
High demand for outbound picking
The project has a fast pace of on-site warehousing, requiring a single station transfer rate of 190 times per hour, with an average of 1 time in 18 seconds.
High requirements for positioning accuracy and stopping accuracy
Adjacent shelves have a small front, rear, left, and right spacing and they are closely arranged. At the same time, they need to be docked with the manipulator. The AGV positioning accuracy and stopping accuracy are required to reach ±5mm.
Lots of materials to be transported and complex site
The operation site is small and the number of AGVs is large, which greatly tests the dispatching ability of the AGV control system.
Solution
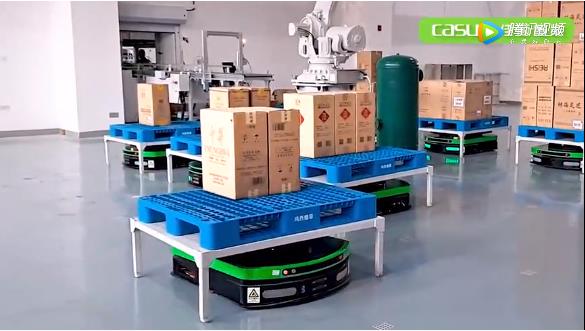
The project used 15 C2-23 latent backpack-lift AGVs, 2 sets of automatic charging columns, 1 set of automatic stacking machines, 1 set of dual-machine hot backup software and hardware, and six-axis robotic arms.
◆The AGV intelligent control system is docked with the customer’s WMS system and the manipulator operating system to intelligently plan the optimal transportation path of the AGV, and improve the efficiency of in and out of the warehouse and the efficiency of picking and stacking. The delivery volume of the picking out of the warehouse is 18 seconds/time.
◆ AGV transports the finished products into the finished product warehouse in an orderly manner according to the dispatching information.
◆After the warehousing is completed, the manipulator will call the designated product according to the order requirement, and the AGV will take away the designated product of the corresponding warehouse through the AGVS system instruction.
◆The empty tray after disassembly and inspection is automatically docked by the AGV and the tray stacker to realize automatic stacking of the empty tray and transport to the designated location.
Advantages of the scheme
Multi-positioning technology to achieve high-precision docking
AGV uses inertial navigation, visual inspection, and other technologies to achieve precise positioning with an accuracy of ±5mm.
Multi-system linkage realizes intelligent sorting
The AGV intelligent control system is docked with the WMS system to automatically generate inbound and outbound picking tasks, manage the material information of the warehouse in real-time, and realize the synchronization of accounts and materials. Cooperate with the manipulator to realize intelligent destacking without manual involvement in the whole process.
Intelligent scheduling for efficient applications
Intelligently plan the optimal path, reduce invalid walking, and improve operational efficiency. The AGV intelligent control system can also manage the material information of the warehouse in real-time, and realize the synchronization of accounts and materials.
Customer revenue
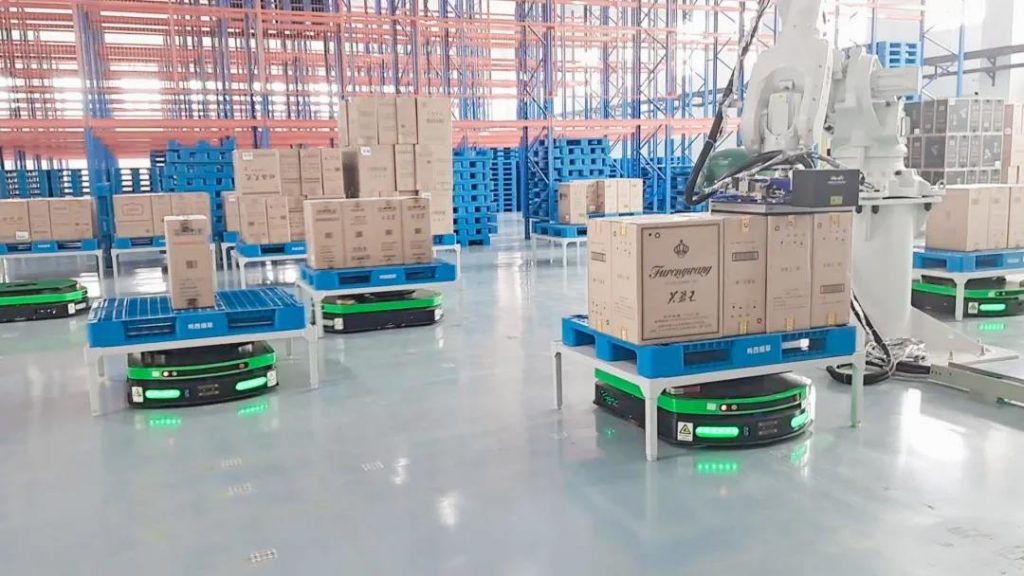
Improve picking efficiency
The AGV performs 190 round-trip operations per hour, with an average of 18 seconds.
Improve storage utilization
Seamlessly connect with the WMS system, realize the optimization of the location, path, and task allocation, rationally plan the warehouse layout, maximize the use of space, and increase the warehouse location by 20%.
Improve information flow
The storage location of the warehouse stores information data, warehousing tasks, and on-site warehousing equipment (manipulators, stackers, warehousing operation terminals, etc.) are managed by the customer’s WMS system to monitor the status of factory materials in real-time.
Reduce labor costs
Reduce the number of operations by personnel, reduce the intensity of manual labor, reduce the rate of operation errors, improve the flexibility of the process, and save a lot of labor costs.
product description
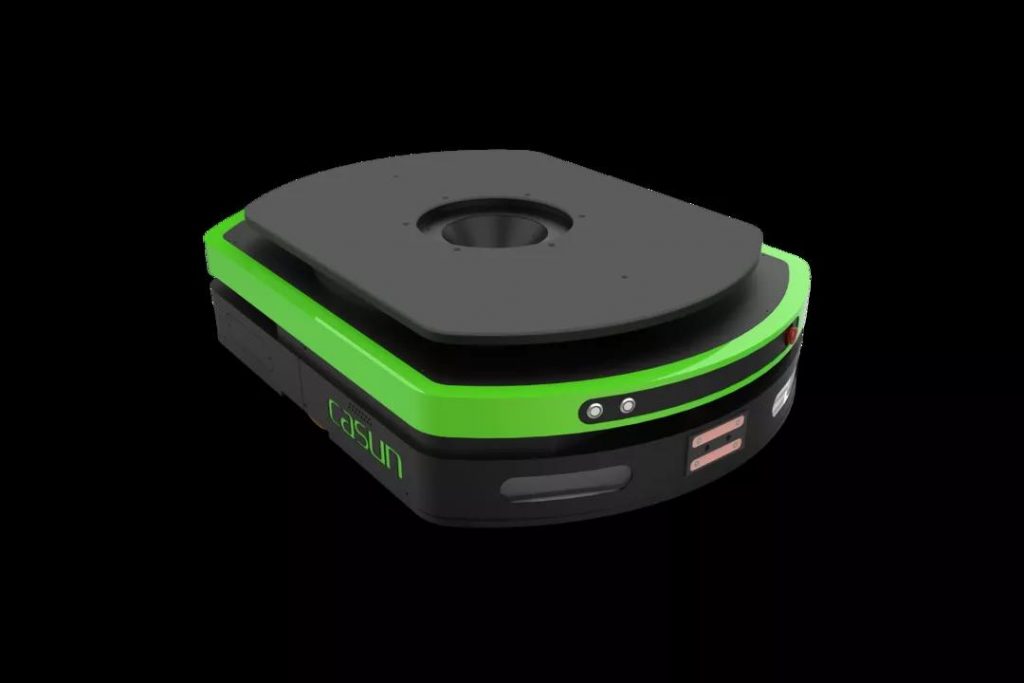
The product used in this solution is a latent lift AGV, one of the star products of CASUN Smart. This QR code navigation AGV has the following nine major advantages:
Strong load capacity
The load capacity can reach 1000KG, and the running speed can reach 90m/min under full load.
Strong environment adaptability
With the function of a self-learning map, the running map can be updated autonomously according to the changes of the scene during operation, thereby greatly improving the environmental applicability.
Can run across regions
It can be docked with various channel equipment such as elevators, electronic doors, and air shower doors to realize cross-floor and cross-regional operation.
High positioning accuracy
The secondary positioning accuracy can reach ±5mm.
High operating efficiency
Using a full servo drive, it can increase the speed quickly (0-90m/s only takes 3 seconds), and has a fast rotation function (only 3 seconds for in-situ rotation).
Cluster scheduling
It is equipped with multiple AGVs to work together to realize the function of cluster scheduling.
Fault self-check
It has a complete fault self-check function and has remote fault diagnosis and self-recovery functions.
Autonomous charging
When the battery is low, it can go to the charging station for automatic charging; no manual intervention is required to achieve 24-hour operation.
Multiple security protection
Equipped with laser obstacle detection sensor, mechanical anti-collision device, and sound and light voice warning to ensure safe operation.