The design of a modern automobile factory is a complex system engineering. As a typical welding factory among the four major processes of the whole vehicle, it not only involves craftsmanship, equipment, engineering, and logistics but also meets the needs of flexibility, high beat, energy-saving, and environmental protection under the trend of product diversification and individualization.
This article combines the project practice of CASUN Intelligent in the automotive industry’s intelligent logistics integrated solution for many years and analyzes the planning director of the intelligent welding factory and the introduction of AGV application.
Contents
- Automobile welding workshop
- The development direction of automobile body welding intelligence
- Key directions of intelligent body welding:
- Intelligent logistics upgrade for body welding
- Planning to establish an intelligent manufacturing management system for welding and assembly;
- It is planned to establish an intelligent logistics system for welded body parts.
- Application of AGV in welding process
- AGV application benefits
- AGV application scenarios
- Application case: welding workshop
Automobile welding workshop
The stamped automobile side panels will directly enter the body-in-white welding assembly line after coming out of the stamping workshop. The welding line is the most complex and most automated production line in the entire automotive production line.
The process structure of the entire welding line is very tight, including spot welding, CO2 welding, stud welding, projection welding, pressing, gluing, adjustment, piping, and a total of 8 processes.
The development direction of automobile body welding intelligence
In the design of automobile architecture, the chassis structure is relatively stable. For the body assembly of the same structure, the structure of the front cabin and floor assembly will not undergo qualitative changes. In order to attract customers, the main change of the body is the upper part. At present, the automation degree of body welding in domestic car manufacturers has been very high. Laser welding, spot welding, arc welding, stud welding, gluing, riveting and other processes are easy to realize machine automation, and the mainline also realizes automatic logistics transportation;
In the development of intelligent manufacturing planning for body welding, it is necessary to combine the actual situation of the enterprise to determine the key development direction of body welding intelligence. Mechanization, automation, informationed, and intelligence are evolving processes. Intelligence must be established on a solid basis. basically.
Key directions of intelligent body welding:
1) Meet the intelligentization of flexible production of multiple types of car bodies;
2) Intelligent monitoring of body welding quality;
3) Intelligent monitoring of welding equipment and tooling status;
4) Intelligent logistics management of workshop parts;
5) Visual prediction, pre-control, early warning, and pre-overhaul of production line equipment mechanical and electrical faults;
Intelligent logistics upgrade for body welding
The intelligent upgrade is a complete set of systematic implementation plans. Auto body welding is upgraded from automated production to intelligent production. It requires the manufacturing planning department to plan and establish welding equipment based on extensive investigation, in-depth analysis, and overall consideration of technological development trends. Intelligent manufacturing management system, to meet the flexible production environment of multiple types of car bodies, to establish a visual intelligent monitoring system for car body welding quality and dimensional accuracy, to establish an intelligent logistics system for welded car body parts, and to establish the visualization of mechanical and electrical failures of the main equipment of the welding line The planning work was carried out creatively in several key areas such as the pre-control mechanism.
CASUN Intelligent has focused on the AGV field for 14 years. As a professional intelligent logistics integrated solution service company, it has a large number of application practices in the automotive intelligent welding workshop. The intelligent logistics upgrade of the welding workshop focuses on the upgraded planning of the following systems.
Planning to establish an intelligent manufacturing management system for welding and assembly;
The intelligent production management system should be connected with the factory’s intelligent manufacturing management system, and be effectively interconnected with the welding intelligent manufacturing unit and the intelligent equipment group, and online issuing and receiving various manufacturing instructions, production plans, queue sequences, product specifications, Process parameters, etc.;
Automatic online data collection. Online inspection of car body welding process data, including temperature, time, current, voltage, pressure, gluing parameters, etc. related to car body welding; online inspection of sub-assembly geometry, car body geometry, welding fixture status parameters, etc.; intelligent logistics manage. Obtain stamping parts identification, main parts positioning, parts inventory quantity, parts logistics management, error prevention management, etc.;
Through the intelligent manufacturing system, big data analysis and prediction, early warning, correction, etc. of the detected welding data and geometric data are carried out to ensure that the welding strength and geometric dimensions of the car body are qualified and consistent.
It is planned to establish an intelligent logistics system for welded body parts.
The intelligent manufacturing management system is the basis of the intelligent logistics systems and AGV application planning. When carrying out the layout design of the welding workshop, the needs of intelligent logistics should be fully considered, including logistics area, logistics route planning, and AGV automatic online and offline system Wait;
Through the installation of RFID stamping parts racks, subassembly assembly storage transfer shelves, logistics pallets, etc., and the installation of RFID readers at specific locations required to automatically identify, track, locate, and count the transferred parts, these basic Information perception facilities are one of the keys to realizing intelligent logistics;
Through the intelligent logistics system, the AGV is dispatched and managed, the parts in and out of the warehouse are effectively managed, and the empty pallets and racks are managed to meet the needs of flexible production of multiple types of car bodies;
The intelligent logistics system must be connected with the MES system to manage stamping parts and welding sub-assemblies in and out of the warehouse and online management, and deliver them to the consumption point in a timely and accurate manner. Realize the automation and intelligence of the logistics of welded parts.
Application of AGV in welding process
AGV replaces manual handling and realizes automated logistics. AGV has been widely used in the logistics transportation of welding workshops, replacing traditional manual transportation of materials and transportation vehicles and equipment such as battery trucks, forklifts, belt conveyors, and buffers.
AGV application benefits
Save manpower and reduce errors;
The application of AGV has changed the logistics and transportation mode, not only realizing labor-saving but also reducing material supply problems caused by human error;
Reduce safety risks;
AGV replaces battery trucks, forklifts, and other operating vehicles, greatly reducing the potential safety hazards caused by human-computer interaction;
Save space and improve space utilization; The flexibility of AGV solves the problems of traditional transmission tools that occupy a large space and are difficult to transform. Logistic transportation mostly uses traction AGV, which is small in size and low in price. It is used in conjunction with a truck with casters to transport the truck to a designated location. The AGV feeder can be made into a one-piece structure or an integrated structure (feeder pallet + appliance).
AGV application scenarios
Accurate docking of AGV and robot docking
After the AGV cart is in place if the parts are manually loaded, the accuracy of the AGV itself can be satisfied; if the robot automatically grabs the workpiece from the cart, the robot has a high requirement for the position accuracy of the workpiece. In order to achieve automatic reclaiming: generally change With the feed opening structure and the addition of visual recognition, the CASUN AGV can achieve precise positioning of ±5mm, which ensures the precise docking with the robot;
Application of AGV in adjustment line
Traditional welding adjustment lines usually use fixed roller conveyors, and each time the model is added or the position is modified, the workload is very large, and even needs to be dismantled and rebuilt. In order not to affect the production of the models in production, the transformation time is usually very short and the transformation is difficult. Big.
AGV replaces fixed rolling bed in the adjustment line application, design multi-model general pallets or directly switch pallets to meet the requirements of high flexibility in the production line; because the position of the AGV trolley is not fixed, the production site can be changed at will, breaking the line body pair The fixed demand mode of space.
AGV switch fixture to realize production adaptation
The traditional automobile welding production line is a linear production structure. This production model is based on the same platform models. When different platform models are mixed, it will lead to unbalanced use of process equipment.
The application of AGV brings the possibility to realize the mixed flow function of more models in the production line. In order to meet the mixed demand of more models and increase the flexibility and economy of the production line, the traditional production line is divided into modules according to functions, and workstations with different functions are established. According to the process requirements of different models, enter the corresponding workstations. Others are not involved. The work station is closed or the production of other models is carried out at the same time, which not only saves production time, improves the utilization rate of the equipment, but also reduces the cost of single-vehicle production.
The AGV can also be used to switch fixtures, grippers and another tooling. Before production, the tooling and fixtures can be transported to the line body with AGV. Any multi-model mixed flow can be realized in the workstation, and the tooling of these different models can be stored in a three-dimensional library offline. , Which greatly reduces the demand for the production area.
Application case: welding workshop
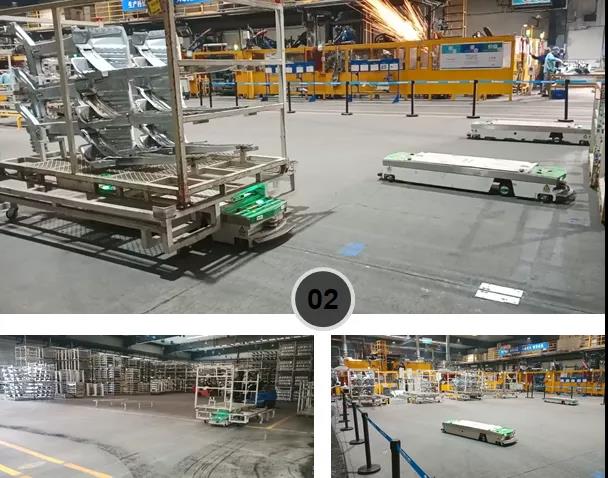
Solution product: C1 latent traction series
Function Description:
1. The AGV system is connected with the production management system to remind warehouse personnel to prepare materials;
2. Realize automatic empty and full material truck exchange;
3. High-precision docking between AGV vehicles and production robots;